Unsliced
GCode Processing for Non-planar Geometries
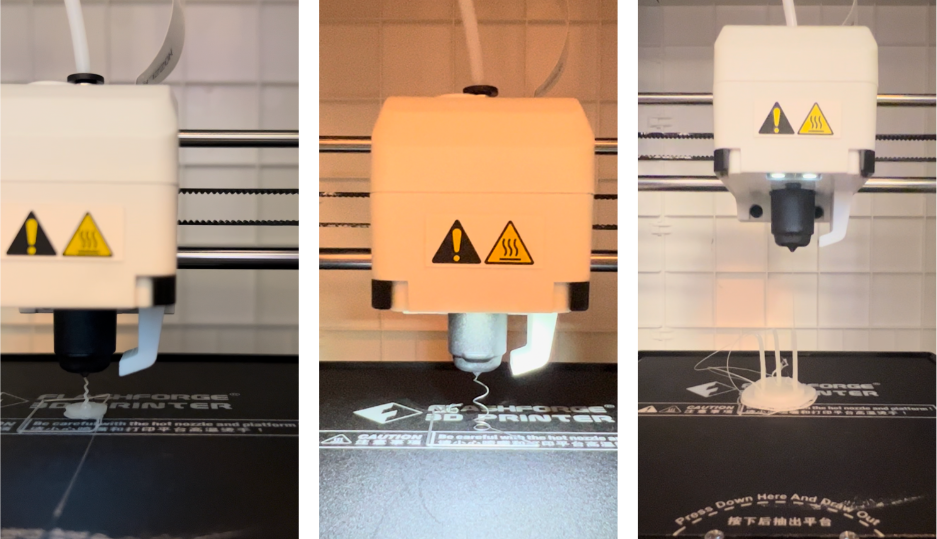
While traditional slicers do print well for the majority of use cases, a significant number of geometries that are difficult to print could be made readily available if printers could alternate between layer-by-layer printing and vertical or angled printing. Approaches to address this issue have broadly taken the name 'universal slicing' which refers to combining the litany of possible alternatives to layer-based printing that researchers and designers are exploring. While many non-planar geometries would benefit from universal slicing, I explored two in particular. The first structure, a small table or stool, supported by vertically printed legs, demonstrates the difference in tensile strength of the structures when printed with a traditional slicer and when printed with the novel approach. While the traditionally sliced leg is brittle and weak, the vertically extruded leg is flexible and durable. The second structure, a spring, demonstrates another property that can be achieved with universal slicing that cannot be implemented well with layer-based printing. While a typical 3D printed spring in PLA is predominantly rigid, due to the stacked plates that comprise the coil, the continuously extruded coil exhibits the typical bounce and springiness that we would expect from a small aluminum spring.
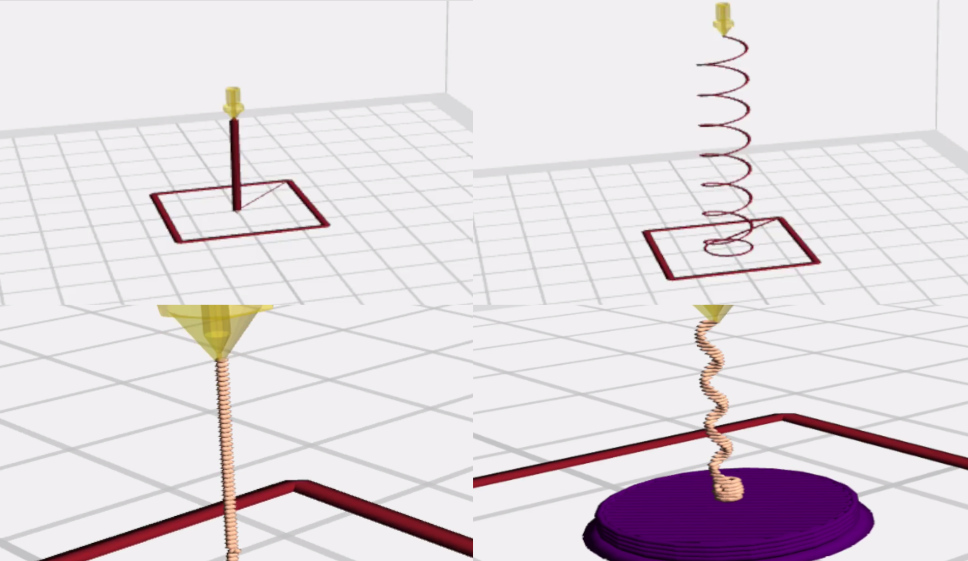
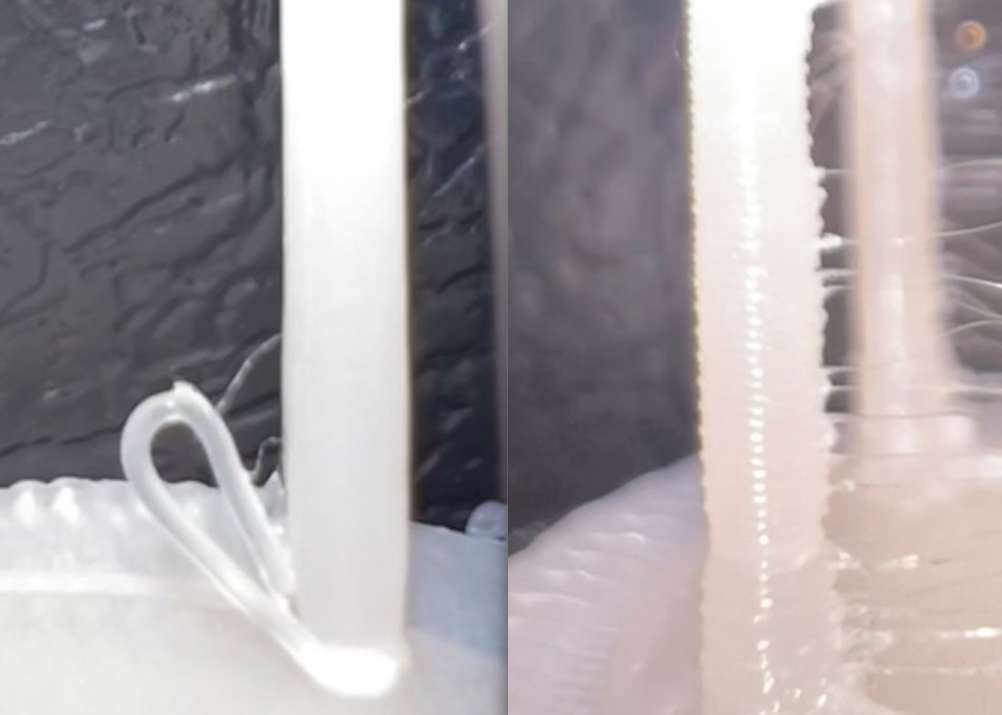
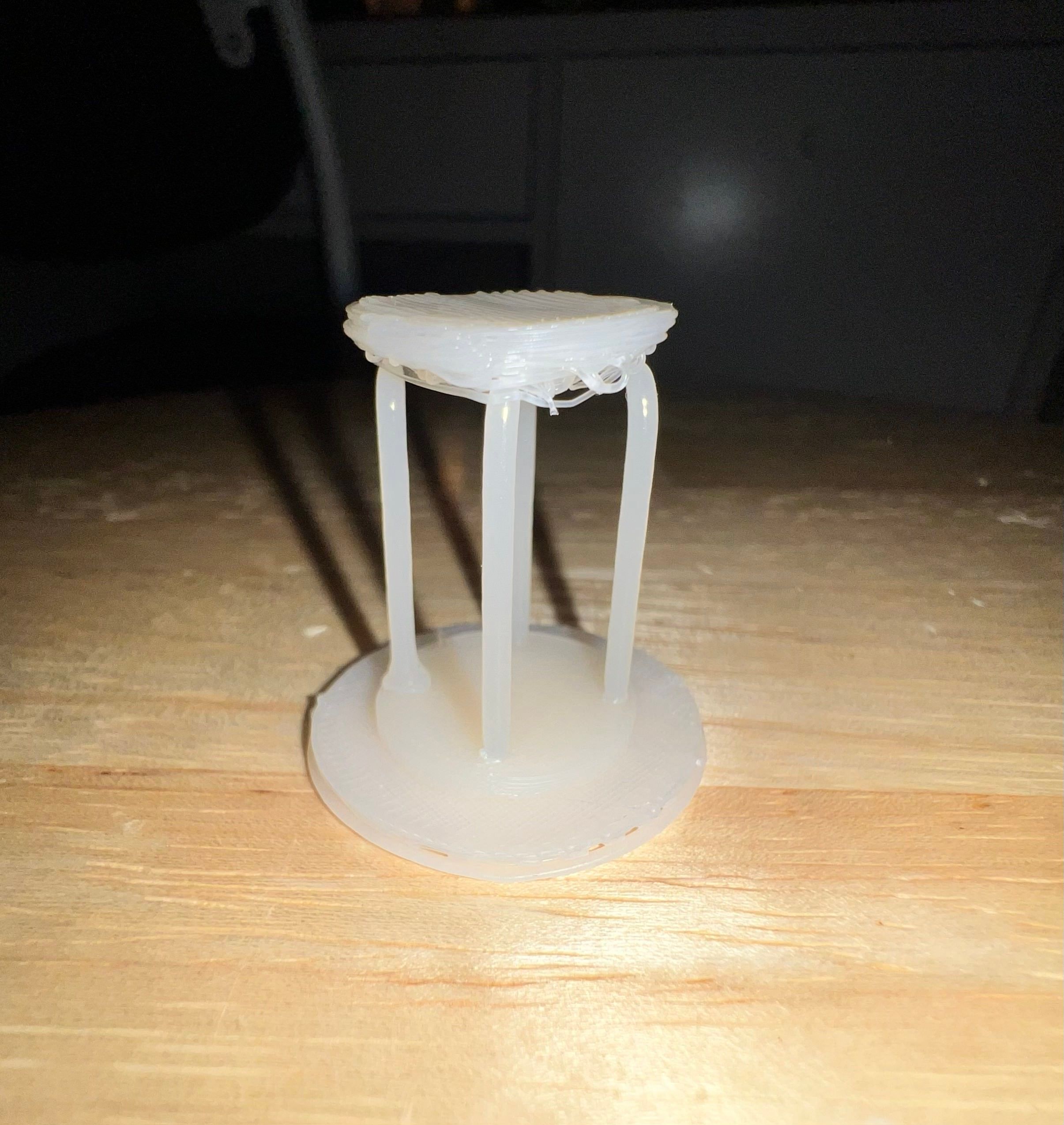
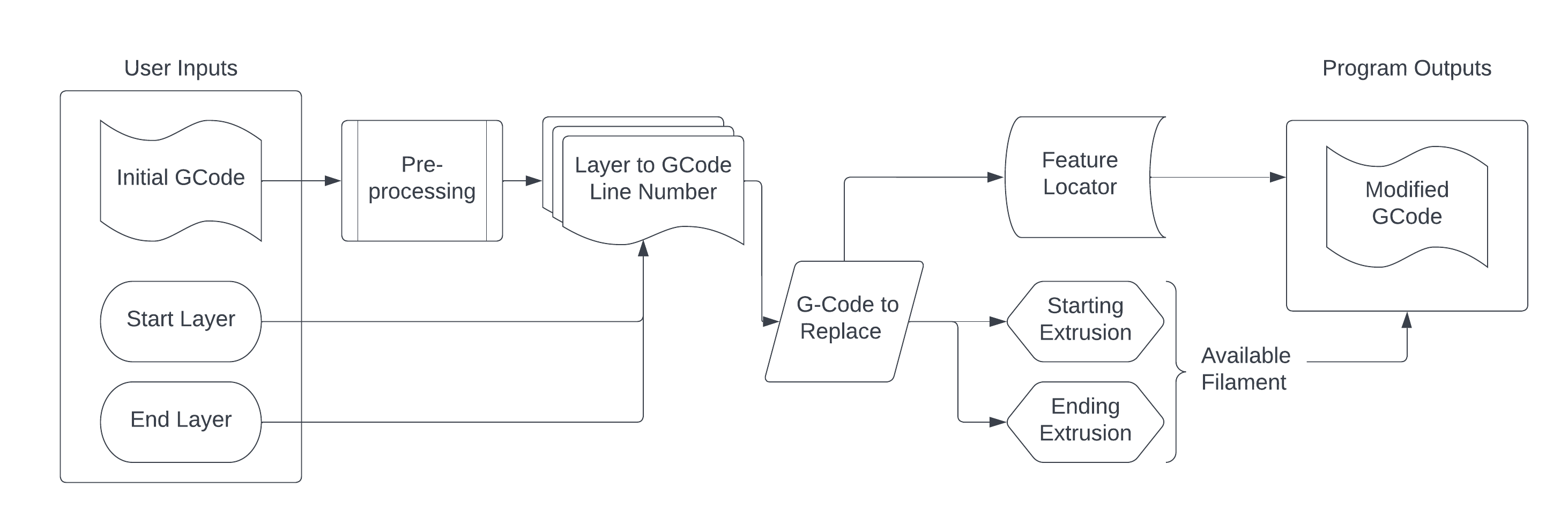